The mixing screw of the mixer is generally made into a double-layer structure. During operation, the outer screw collects the material from both sides to the center, while the inner screw pushes the material from the center to both sides, forming convective mixing. Spiral belt mixer is generally used for mixing viscous or cohesive granular materials, as well as for mixing materials that require the addition of liquid or paste in the granules; Due to the difficulty in cleaning viscous materials, they are often used in situations with high production and infrequent variety changes.
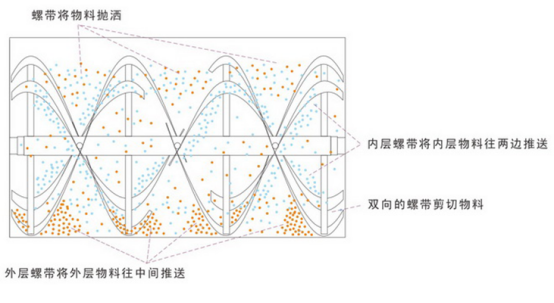
1. The U-shaped horizontal cylinder structure ensures minimal movement resistance of the mixed materials (powder, semi fluid) inside the cylinder.
2. The inner and outer double-layer spiral belts turn in opposite directions and are installed on the same horizontal axis, forming a low-power and high-efficiency mixing environment. The outer spiral belt collects materials from both sides to the center, while the inner spiral belt pushes materials from the center to both sides. The materials form more vortices in the flow, accelerating the mixing speed and improving the mixing uniformity.
3. The stirring screw belt can be made into a blade type and can also be equipped with a flying knife to adapt to different materials; The cylinder can be made into a circular shape, capable of bearing pressure, and used for material reaction and drying treatment.
4. The cylinder cover can be made into an arch shape or a fully open shape. The arch shape can withstand pressure, while the fully open shape is convenient for cleaning.
5. Suitable for mixing viscous materials, it can maintain the integrity of granular materials as much as possible. Materials with a ratio difference of 1:1000 to 10000 can also be mixed well. It can also stir paste like, viscous or high specific gravity materials (such as putty, real stone paint, metal powder, etc.).
3、 Technical parameters
Widely used in industries such as chemical, food, building materials, and pharmaceuticals
for the mixing of solid (i.e. powder to powder) and slurry (i.e. powder to slurry) putty, real
stone paint, dry powder, putty, feed, ceramics, refractory materials, etc., especially suitable
for the mixing of viscous materials. This mixer is not suitable for mixing materials with high
fiber content and significant density differences. In general, for dry powder sand slurry
containing vitrified microbeads, it is recommended to use a horizontal screw belt mixer.
1. Firstly, determine the volume of each batch of mixed materials within the range of 0.1-20
cubic meters and select equipment of the corresponding specifications.
2. Select equipment materials based on material characteristics, and choose corresponding
materials according to the contact and non-contact parts with the material. Conventional
materials include carbon steel, 304/316L/321 stainless steel, etc. Based on factors such as
material properties, working conditions, and hygiene levels, determine the surface treatment
requirements for the material.
3. According to the properties such as material density and fluidity, as well as the equipment
start-up method, power is configured. The start-up methods are divided into heavy-duty
start-up and no-load start-up.
4. Based on the actual process situation, should auxiliary functions such as liquid spraying,
heating/cooling be added to the surface.
5. Reasonably design the opening requirements of equipment, such as feeding ports,
cleaning ports, exhaust holes, and corresponding cleaning methods.
6. Choose the appropriate discharge valve group and driving method, which can be manual,
pneumatic, electric, etc.
Hot Tags: Horizontal screw belt mixer Screw belt mixer WLDH horizontal screw belt mixer